Surface finishing
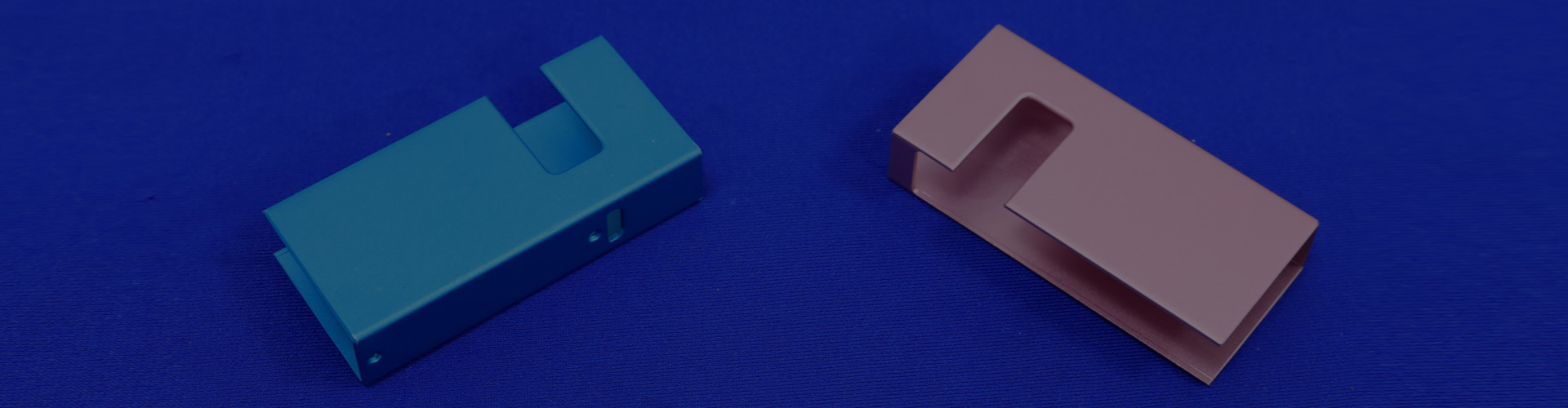
表面处理是指使原型零件的表面具有特定外观的不同过程,以赋予其独特或所需的外观和感觉。使用不同的技术来达到效果。
伯丰为通过不同制造方法生产的所有组件和零件提供高质量的表面处理服务。我们拥有一支技术娴熟的团队,他们以正确和专业的方式进行工作。
表面处理
高光抛光(High Gloss Polishing)
打磨抛光是原型制作中最常见的表面处理之一。打磨是去除切割痕迹或印刷痕迹以获得光滑表面的基本过程。准备好进行进一步的表面处理,例如喷砂、喷漆、镀硌...... 从粗糙的砂纸开始,当您达到2000砂纸时,零件表面足够光滑,可以进行高光抛光,以获得光泽的表面或者镜面外观、透明;如导光板、透镜。
喷漆(Pointing)
喷漆是创建不同曲面外观的一种非常灵活的方法。我们可以实现:哑光、缎面、高光、纹理(轻 & 重)
喷粉(Powder coating)
喷粉是一种干式涂装工艺,自1960年代在北美推出以来就变得非常流行。喷粉工艺占整个工业表面处理市场的15%以上,用于各种产品。越来越多的公司指定喷粉工艺以获得高质量、耐用的表面,从而最大限度的提高产量、提高效率并简化环境合规性,喷粉工艺用做功能性(保护性)和装饰性饰面,将具有无限的颜色和纹理范围。
染色(上色)
染色是将染料或者颜料应用于一种材料,目的是获得具有所需色度的颜色。染色通常在含有染料和特殊化学材料的特殊溶液中进行,适合着色的材料:ABS、PMMA、PC、PS。
阳极氧化(Anodizing)
阳极氧化是电子产品创造体面表面最流行的方法。Apple几乎在所有的产品中都使用了阳极氧化处理。
丝印(Silk-Screen Printing)
丝印是最流行的印刷技术之一,也是公司在不同尺寸和材料的产品上印刷设计时最常用的技术。丝印是一种模块印刷方法,涉及通过模块印刷油墨,这些模板由拉伸在称为丝网的框架上的多孔织物网支撑。丝印非常适合大的图形设计。
移印(Pad Printing)
移印工艺是一种间接胶印工艺,其中图像通过柔软的硅胶垫转移到要印刷的表面上。
激光雕刻(Laser Engraving)
激光雕刻是激光束物理去除材料表面以露出空腔的过程,该空腔在与眼睛齐平时显示图像。激光在雕刻过程中会产生高热量,这基本会导致材料蒸发。
喷砂(Blasted)
喷砂会在机加工零件上添加均匀的哑光或缎面表面光洁度,从而去除加工痕迹。这主要用于视觉外观处理,有几种不同的粒度,从而表示喷砂颗粒大小。
电镀(Plating)
电镀是金属沉积在导电表面上的表面覆盖物。电镀用于装饰物体、抑制腐蚀、提高可焊性、硬化、提高耐磨性、减少摩擦、提高油漆附着力、改变导电性、提高红外反射率、用于辐射屏蔽和其他目的。
蒸汽抛光(Vapor Polishing)
这是一种专门的处理方法,我们用它来使零件更加的明亮和清晰。主要是聚碳酸酯(PC)塑料。我们也可以用这种方法来修复零件表面的小缺陷。这个过程可以制作出 非常好和清晰的表面、形状复杂的零件或难以触及的区域。
蒸汽抛光示例:小心地将零件打磨到#1500粒度,然后放置在大气控制的环境中。之后,使用Weldon4气体在分子水平上熔化塑料表面,然后所有小划痕都会变得越来越清晰。